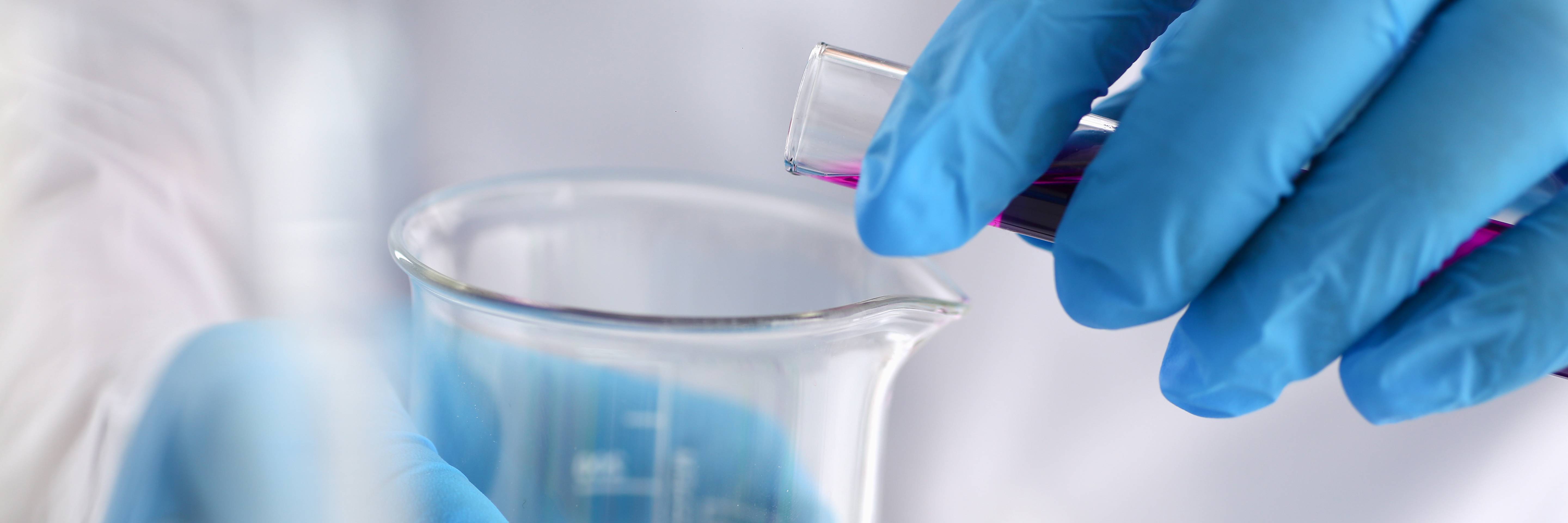
Kao Collins Inkjet Inks Reduce Risk of Ink Migration
Download
Rarely a week passes without news about a food product recall, often for bacterial contamination, which puts consumers at risk and the reputation of companies on the line.
Food producers, large and small, can’t afford to ignore any part of sourcing food contact materials (FCMs) – including product packaging.
In 2005 the Swiss-based food giant, Nestlé, faced headlines like “Baby milk scare widens in Europe.”
The company ordered the recall of 30 million liters of baby milk after testing revealed a chemical in the printing ink leached through the packaging.
The packaging used a UV-curable ink that contained a photoinitiator, isopropyl thioxanthone (ITX), that reacted with sunlight’s ultraviolet waves, migrating through the package into the milk’s fatty products.
A multitude of rules and regulations
Article Index
Right out of the gate, the first thing to understand is that there is no “FDA Approved Ink.” That’s not unique either. If it were that simple, every ink manufacturer would be promoting their “FDA Approved!” ink.
Government agencies around the world regulate food safety. Additionally, major food manufacturers have developed detailed requirements for companies in the supply chain, including Nestlé. The company publishes its Nestlé Quality Requirements for Vendors of Raw and Packaging Materials, considered a benchmark for packaging quality.
Switzerland publishes a list of food-grade chemicals or ingredients for inks that can be used for food packaging. These are starting points for passing the regulatory hurdles.
Inks must be evaluated and tested for each food product and potential interactions. Every food is different. The packaging varies. The environmental conditions of consumer storage, handling, and cooking play a part in how food ingredients interact with packaging.
Ink is called “food-grade” if it is safe for human consumption and can come in direct contact with food. For the ink to be used, there must be testing for it to be considered “food-safe.”
How the food-grade ink interacts with the packaging substrate, the nature of the food itself, consumer use, and various environmental factors are just some lab testing that must be done. The “food-safe” has stricter requirements.
Food-safe means the ink for packaging is safe for direct food contact under-identified and tested conditions.
For example, an ink may be food-safe if not subjected to heating in a microwave oven or exposed to sunlight.
Inks for food contact packaging must undergo rigorous third-party lab testing to ensure it is food-safe. Ink manufacturers must involve the chemists, toxicologists, packaging engineers, and the details of the source materials.
Food safety requires a 360-degree production process.
Managing quality and food-safe inks around the world
While the opportunities for inkjet ink in food packaging expand, manufacturers in the supply chain must comply with a dizzying array of time-consuming and costly hurdles.
The following is intended to be a brief overview of regulatory oversight and not a complete deep dive into the approval of food-packaging coatings.
Types of Ink Migration – 3 ways Packaging Inks Compromise Food Safety
- Migration – Ink components that pass through the substrate
- Invisible set-off – Transfer of ink components from the printed side to the food-facing side during printing or spooling
- Gas-phase transfer – Volatile ink substances interact with the air in the packaging.
Managing and maintaining quality across the food-production chain is critical for food safety.
Across the globe, manufacturers in the food industry may be navigating general safety standards, positive chemical/additive lists, and required and voluntary standards. Moreover, the requirements continue to change.
Never miss Ink Tank’s informative articles. Sign up for our email.
FDA Food Packaging Compliance in the U.S.
If a coating, such as ink, in food packaging is expected to become a food component, the U.S. Food and Drug Administration (FDA) has specific regulations. Before going to market, the coating must meet one of these five clearances for compliance or authorization:
- Substances permitted by an effective Food Contact Notification (FCN). This is the FDA process for a manufacturer or supplier to submit information about the identity and use of a food-contact material that it is safe for the intended use based on chemistry and toxicology testing.
- Substances permitted by regulation in 21 CFR 175, 176, 177, 178.
- Generally Recognized As Safe Substances (GRAS) as determined by FDA. Some GRAS may be limited to a specific intended use.
- GRAS substances as determined by qualified experts without FDA approval or notification.
- Substances that fall under prior sanction or approved for use before the Federal Food, Drug, and Cosmetic Act of 1958.
Swiss Printing Inks Ordinance
Switzerland is the only European country with specific legislation regulating food packaging inks. While the country is a European Free Trade Associatio membern, it is not a European Union Member. Their regulations don’t apply elsewhere in Europe.
Choose Inks for Food Packaging
The Swiss Ordinance only impacts companies selling their products in Switzerland.
The legislation details the positive components of ink chemistry that may be used in formulations. These components are categorized in Annex 10 and include binders (monomers), colorants and pigments, solvents (including energy curing monomers), additives (which does not include those used in the preparation of pigments and aids to polymerization), and photoinitiators.
Annex 10 distinguishes between evaluated substances (Part A) and non-evaluated substances (Part B). The non-evaluated components may be used in formulations if there is no transfer to food above a specified limit.
The Swiss Printing Inks Ordinance doesn’t apply to the following:
- Printing inks directly in contact with food
- Ink migration is impossible such as an aluminum can
- Ink smearing, set-off or transfer via out-gassing can be ruled out
Food-chain manufacturers do not have to provide compliance documentation before use, but supporting materials must be maintained and available for enforcement review. This includes the condition, testingg results, calculations, modelings, etc.
European Union Regulation of Printing Inks
There is no uniform regulation of food contact materials, such as ink, in the EU. The European Commission signaled that it intends to harmonize disparate regulations among the member states. For years Germany had been pursuing regulation similar to Switzerland. The German government has now put that work on hold in light of the EC announcement.
Across the EU, manufacturers must comply with The Framework Regulation, which establishes a general safety requirement, and that food contact materials (FCMs) must be manufactured in accordance with Good Manufacturing Practices (GMP) so that they do not migrate to food at unsafe levels or change the characteristics of the food.
Requirements prohibit unsafe levels of ink components from transferring to the food-contact side of the packaging.
Once this level of compliance is achieved along with meeting the requirements of one member state, food-packaging inks may be used throughout the EU, based on the principle of mutual recognition.
Additional regulations impact inks through EU’s Regenerated Cellulose Directive, which prohibits contact between the printed surfaces of regenerated cellulose film and food. Also, the Plastics Regulation indirectly includes migration thresholds of printing inks.
Member states have established unique regulations, which make marketing of food products onerous.
China Follows Other Countries
The country of about 1.4 billion people is overhauling the body of standards for FCMs, including inks and adhesives.
Regulations include required GMPs.
The country is looking to the U.S. and EU for the general approach to regulations.
Already, China requires a functional barrier, based on testing, to avoid migration above a strict threshold. Further, FCMs must not be carcinogenic, mutagenic, or toxic for reproduction (CMR). Toxicity data is required, similar to the EU and is tier-based on migration.
Like the U.S. and EU, the use of an FCM requires a petition for clearance. The National Health Commission (NHC) oversees pre-market approval.
A pillar of the system relies on the positive list approach for FCMs, similar to Switzerland, and applies to the entire production chain.
The regulatory body in China defines FCMs as “any materials and products that, under normal use conditions, contact with or are expected to contact with food or food additives (foodstuff), or whose components may migrate into foodstuffs, including packaging materials, containers, utensils, tools and equipment used in manufacturing, processing, packing, packaging, transporting, holding or marketing foodstuff, as well as printing inks, adhesives, lubricating oils, etc. that possibly contact with foodstuff directly or indirectly; excluding detergents, disinfectants, and public water-transportation facilities.”
South America – the Mercosur
A political and economic agreement regulates FCMs in parts of South America. Argentina, Brazil, Paraguay, Uruguay, and Venezuela comprise The Mercosur (Mercado Común del Sur, Portuguese). Chile and Mexico have unique regulations.
Officials in the Mercosur looked to the U.S. and EU for the basis of their FCM regulations. The agreement uses a positive list approach, although there is no specific regulation of inks for non-direct food contact. However, for food safety, the combination of ink and plastic must be evaluated to determine if the products together exceed migration limits.
Direct-contact inks must be formulated using chemistry from the positive lists and comply with metal migration limits.
As in other countries, the production of FCMs must adhere to good manufacturing practices.
Quality Control in Food Packaging and Production
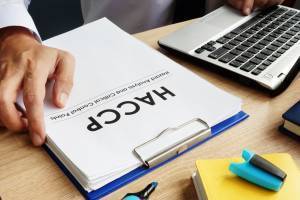
Hazard Analysis and Critical Control Points (HACCP) systematically address food safety.
Food companies are adopting quality management programs. The internationally-recognized Hazard Analysis and Critical Control Point (HACCP) is a system for addressing food safety through the analysis and control of biological, chemical, and physical hazards from raw material production, procurement, and handling, to manufacturing, distribution, and consumption of the finished product.
7 principles of the HACCP system.
- Conduct a hazard analysis.
- Determine the critical control points (CCPs).
- Establish critical limits.
- Establish monitoring procedures.
- Establish corrective actions.
- Establish verification procedures.
- Establish record-keeping and documentation procedures.
Food brands may require certification of suppliers through this quality management system.
HACCP began as a quality assurance program at Pillsbury in the 1960s while producing food for astronauts in the fledgling NASA program. Various reputable science organizations have endorsed HACCP, including The National Academy of Sciences, National Advisory Committee for Microbiological Criteria for Foods.
See Inks for Food Packaging
Get StartedIt is difficult, time-consuming, and costly to establish the safety of inks used in food packaging. It is incumbent on the ink manufacturers and their suppliers to demonstrate this through strenuous lab testing for specific use cases of the coating. While GRAS determinations provide an initial benchmark, they carry some risk and require evaluation.
The Maze of Food Safety
As Nestlé discovered, the ink used for baby milk reacted in unintended and unforeseen ways.
Ink is but one piece of the food-safety puzzle. Chemists and engineers must evaluate a multitude of factors in food manufacturing to ensure consumer safety. Besides the chemistry of the ink, the substrates must be uniquely evaluated and in combination with the ink chemistry.
Considering the infinite number of food possibilities, testing of FCMs is done on simulated food that mimics the characteristics of actual food. Using standardized simulated food ensures more consistent results. Acidic food may react differently from a high-fat product.
Beyond how the chemistry of the food contact material reacts directly with the food, environmental and other factors must be evaluated, such as heating, freezing and long-term storage, etc. While it is difficult to foresee all possible use factors, food safety depends on anticipating the “what if” question.
What Inkjet Inks can be Used for Food Packaging?
The first question to ask is whether the ink is in direct food contact or indirect contact.
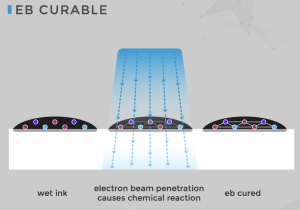
EB curing uses significantly less energy than UV curing.
Electron Beam (EB) Inkjet Inks
These inkjet ink formulations have a distinct advantage over UV or LED light-curing inks because electron beam (EB) inks don’t require the addition of photoinitiators. The powerful electron beam completes the polymerization process. There are other benefits of EB inks for food and pharmaceutical packaging. EB inks may be less expensive because they don’t require photoinitiators. They don’t require solvents for cleanup, a plus for the environment and food packaging. Because ink migration is a primary concern for food and pharmaceutical packaging, EB inks stand out for low migration. Also, the electron beam operates cooler than other curing systems, making it a viable option for flexible packaging and thin films.
UV Inkjet Inks
A UV ink is generally not suitable for packaging if there is direct food contact because of the pigments and oligomers, a type of polymer used in the inks. If the ink is used atop a functional barrier that prevents migration, a UV ink may be used. Since consumer safety and corporate reputation are at stake, testing should rule out potential circumstantial risks.
Depending on the type of packaging, UV curing must be evaluated for potential ink migration from set-off smearing on the food-facing surface.
Low-migration UV/LED Inkjet Inks
Newer photoinitiators and ink solutions offer UV ink formulations with lower levels of migration. With there being a potential for ink migration, testing should be done to verify the safety of the FCM. Kao Collins formulates low-migration UV/LED curable inks.
An essential factor for any UV ink is curing. Without complete curing, an ink may not comply with regulations despite performing optimally in a lab setting.
Eco-friendly Water-based Inkjet Ink
Manufacturers continue to develop innovative inks. Kao, for example, has developed LUNAJET, a water-based, eco-friendly ink being used for shrink sleeve labels, flexible food packaging, and films. The ink offers a solution for manufacturers focused on consumer safety, high image quality, adaptability, and sustainability. It fits into consumer demand for these new types of product packaging.
Swiss-Compliant Solvent Inks for HP
Swiss-compliant SIGMA solvent inks for non-porous materials support high-quality using HP printing systems. The SIGMA yellow ink extends marking and coding options to dark surfaces. The other SIGMA colors produce consistent printing results on lighter surfaces.
Digital Future of Food Packaging
For a variety of reasons, digital printing offers new opportunities for food packaging.
While lab testing requires considerable time and cost, the opportunities for using inkjet printing are increasing.
Manufacturers trying to appeal to regional interests, product variations or limited releases, are increasingly using digital technology, which offers the flexibility of shorter production runs and customization.
Also, inkjet inks for food packaging contribute to sustainability efforts. Labels can often be eliminated because digital printing can be done directly on the packaging. While it seems small, a label requires natural resources for production, transportation, and warehousing.
The food-grade inks themselves reduce environmental impact. Low-migration UV inks have fewer toxic components. Until now, that was the best type of ink for food packaging.
Kao’s LUNAJET and EB curable inks achieve greater sustainability because they can be printed directly on the packaging and, unlike UV formulations, don’t require photoinitiators.
See Inks for Food Grade Printing
Get StartedFood producers, trying to appeal to consumer demands, see inkjet printing for their packaging as a cost-effective solution for introducing test products or a wider range of flavor offerings. Digital printing offers food companies the option of bringing unique packaging designs and messaging to market more quickly – and safely.
Kao Collins works with printers, packaging designers, and FCM producers to create custom ink formulations. Contact us to help create ink formulations for possible use in the food-packaging chain.
READ MORE
Shrink Sleeve Labels for food packaging in the Age of Inkjet
How EB Inks are Changing the Printing Industry
Water-Based LUNAJET Ink Ideal for Printing on Flexible Film Packaging
WATCH
Download Our Guides to Inks for Improving Performance
Frequently Asked Questions – FAQs
Ink is called “food grade” if it is safe for human consumption and can come in direct contact with food. For the ink to be actually used, there must be testing for it to be considered “food safe.”
.
What is an FCM?
FCM is short for Food Contact Materials. It is any product or substance that comes in contact with food. Interactions of FCMs, when combined, must be evaluated.
What is GMP?
It is short for Good Manufacturing Practices and comprises the operational or production requirements for the food industry to maintain consumer safety. It is a pillar of the HACCP system.
The ink for packaging is safe for direct food contact under-identified and tested conditions.
- Penetration Migration – Ink components that pass through the substrate
- Invisible set-off – Transfer of ink components from the printed side to the food-facing side during printing or spooling
- Gas-phase transfer – Volatile ink substances interact with the air in the packaging.
It is the transfer or bleed-through of ink substances from the packaging material into a product such as food, medicines, or health and beauty.
Food Contact Notification (FCN) is the U.S. Food and Drug Administration (FDA) process for a manufacturer or supplier to submit information about the identity and use of a food-contact material that it is safe for the intended use based on chemistry and toxicology testing
Food Contact Materials are any product or substance that comes in contact with food. Interactions of FCMs, when combined, must be evaluated.
Good Manufacturing Practices (GMPs) comprise the operational or production requirements for the food industry to maintain consumer safety. It is a pillar of the Hazard Analysis Critical Control Point (HACCP) system.